- GD&T
GENERAL DIMENSIONING- International Paper Size Standards
- Technical Drawing Styles
- ISO And ANSI Projections
- ANSI Technical Drawing Views
- Technical Drawing Dimesioning Types
- ANSI and ISO Geometric Tolerancing Symbols
- Geometric Tolerancing Reading
- Taylor Principle Rule#1
- Form Tolerances
- Profile Tolerances
- Orientation Tolerances
- Location Tolerances
- Runout Tolerances
- TOLERANCES
ANSI AND ISO- Tolerancing and Engineering Standards
- Hole and Shaft Basis Limits And Fits
- ISO International System For Limits And Fits
- International Tolerance Grade (IT)
- Fundamental Deviations For Hole and Shaft Basis
- ISO Tolerance Band IT01-IT16
- Calculation Of International Tolerance
- Calculation of Upper and Lower Deviation For Shaft
- Calculation of Upper and Lower Deviation For Holes
- ISO Shaft Tolerances (3mm-400mm)
- ISO Shaft Tolerances (400mm-3150mm)
- ISO Hole Tolerances (3mm-400mm)
- ISO Hole Tolerances (400mm-3150mm)
- ANSI Standard Limits and Fits
- METAL CUTTING TECHNOLOGIES
- Terms and Definitions of the Cutting Tools
- Cutting Tool Materials
- Selection of Carbide to machine the work-part
- Identification System For Indexable Inserts
- Work-Part Materials
- Machinability and the specific cutting force
- Machinability of the Certain Material Evaluations
- Cutting Forces and Chip Formations
The Importance of the Using Proper Coolant when cutting Titanium and its alloys
A low coefficient of friction is
developed by using proper coolant delivery. This results in lower temperature so the workpiece doesn’t
get soft and tool life is extended. Under pressure and direction, the coolant knocks chips off the cutting edges
and provides anti-corrosive benefits for machine tool and work. There is a high correlation between the amount of
coolant delivered and the metal removal rate. To optimize the performance of the cutting tools, they must be adequately
cooled. With the proper coolant flow, tool life and higher maximum effective cutting speeds can be reached. In Milling
and Turning processes, applying coolant using our newest technology ( coolant
delivered at the cutting edge, through-the-tool coolant, or coolant nozzles to each insert) is an optimal
way to increase tool life and maximize productivity. Coolant nozzles direct a concentrated stream of coolant
to the cutting edge, providing multiple benefits. First, the cutting edge and workpiece are kept as cool as possible.
Second, the cutting edge and workpiece are also lubricated for a minimum coefficient of friction. Finally, the coolant
stream effectively forces the cut chips away from the cutting edge, thereby eliminating the possibility of recut chips.
Provide a generous “volume” of coolant when machining titanium, and when applying drills and mills
in a vertical application to improve chip evacuation and increase tool life. It is important to use a high
coolant concentration to provide lubricity, which will aid in tool life, chip evacuation, and finer surface
finishes. High-pressure coolant, either through the tool or through a line adjacent and parallel to the tool,
should always be considered for increased tool life and production. Do not use multi-coolant lines. Use one
line with 100% of the flow capacity to evacuate the chips from the work area. Use synthetic or semi-synthetic
at proper volume, pressure, and concentration. A 10% to 12% coolant concentration is mandatory. Through-coolant
for spindle and tool can extend the tool life by four times. An inducer ring is an option for through-spindle flow.
Maximize flow to the cutting edges for best results. At least 3 gal/min (13 liter/min) is recommended, and at least
500 psi (35 bar) is recommended for through-tool-flow.
Metallurgy of Superalloys
High-temperature alloys derive their strength from solid solution hardening, gamma prime precipitation
hardening, or oxide dispersion strengthening. Metallurgy is controlled by adjustments in composition
as well as through processing, including the aging treatment where the solution-annealed alloy is
heated until one or more phases occur. The resulting austenitic matrix combined with a wide variety
of secondary phases such as metal carbides (MC, M23C6, M7C3), γ´, the ordered fcc strengthening phase
(Ni3 [Al, Ti]), or the γ˝ (Ni3Nb) impart to the alloys their excellent high-temperature strength.
Superalloy components are typically available in cast, wrought (forged), and sintered (powder metallurgy)
forms. Some important characteristics to consider about each form; Cast alloys have coarser grain sizes
and exceptional creep strength. Wrought alloys have more uniform and finer grain sizes and possess higher
tensile and fatigue strength. Powder metallurgical processing enables production of more complicated and near-net shapes
Machinability of Superalloys
Superalloys generally have poor machinability. The very characteristics that provide superior high-temperature
strength also make them difficult to machine. Additionally, decreased cutting tool speeds can limit productivity.
The main challenges to machining superalloys include: The high strength of nickel-base superalloys at cutting
temperatures causes high cutting forces, generates more heat at the tool tip (compared to alloy steel machining),
and limits their speed capability. The low thermal conductivity of these alloys transfers heat produced during
machining to the tool, subsequently increasing tool tip temperatures and causing excessive tool wear, which can
limit cutting speeds and reduce useful tool life. The presence of hard, abrasive intermetallic compounds and
carbides in these alloys causes severe abrasive wear on the tool tip. The high capacity for work hardening in
nickel-base alloys causes depth-of-cut notching on the tool, which can lead to burr formation on the workpiece.
The chip produced during machining is tough and continuous, therefore requiring acceptable chip control geometry.
In addition to the challenges mentioned above, the metallurgical route by which the components are produced also
affects their machinability. These materials are easier to machine in the solution annealed (soft) condition than
in the heat-treated (hard) condition. Furthermore, under similar conditions of heat treatment, the iron-nickel-base
superalloys are easier to machine than the nickel-base or cobalt-base superalloys. Finish machining is critical for
aerospace components because the quality of the machined surface may influence the useful life of the components.
Great care is taken to ensure that there is no metallurgical damage to the component surface after the final finishing pass.
Machining Superalloys with CARBIDE tooling
PVD coated carbide tools with positive rakes are suitable for finishing
and medium machining. — Reduces cutting forces and temperatures Minimizes part deflection. Always maintain high feed-rate and depth
of cut. Minimizes hardening, Use a generous quantity of coolant with carbide tools. Reduces temperature build-up and rapid tool wear,
utilize high-pressure coolant whenever possible. For rough cutting, T-landed ceramic inserts are recommended, with carbide inserts,
use moderate cutting speeds. Minimizes tool tip temperatures and encourages longer tool life, Never allow tool to dwell.
Minimizes possibility of work hardening and subsequent problems are in downstream process.
Machining Superalloys with CERAMIC tooling
Higher cutting speeds of 600–4000 SFM are possible with ceramic tools
(SiAlON and SiC whisker-reinforced Al2O3). There is no need for coolant. Depth-of-cut notching is more pronounced
(versus carbides). When notching is severe (primarily in roughing cuts on forgings with scale), use higher lead angle.
Reduces tool pressure and work hardening and improves surface finish.
Machining Superalloys with PCBN tooling
Use low-content PCBN grades for finishing and semi-finishing at
low depth of cut, but optimize the cutting conditions for each individual part, and pay close attention to surface condition.
Use sharp edge uncoated grades for better surface finishes and close tolerance, Use coated grades to increase tool life and productivity.
There are some machining challenges with Superalloys
High-Temperature Alloys have a low thermal conductivity, meaning heat generated during machining is neither transferred
to the chip nor the workpiece, but is heavily concentrated in the cutting-edge area. These temperatures can be
as high as 1100°C to 1300°C and can cause crater wear and severe plastic deformation of the cutting tool edge.
Crater wear can, in turn, weaken the cutting edge, leading to catastrophic failure. Crater wear resistance
is an important tooling property requirement for machining High-Temperature Alloys. Plastic deformation,
on the other hand, can blunt the edge, thereby increasing the cutting forces. Retention of edge strength at
elevated temperatures is also a very important tooling requirement while machining High-Temperature Alloys.
The chemical reactivity of these alloys facilitates formation of Built Up Edge (BUE) and coating delamination,
which severely degrades the cutting tool, leading to poor tool life. An ideal cutting tool should exhibit
chemical inertness under such extreme conditions. The hard, abrasive intermetallic compounds in the
microstructure cause severe abrasive wear to the tool tip. The chip produced in this machining is tough
and continuous and requires superior chip breaker geometry. Heat generated during machining can alter the
alloy microstructure, potentially inducing residual stress that can degrade the fatigue life of the component.
ISO H; HARDENED STEEL
This group of materials contains hardened and tempered steels with hardnesses greater than 45 – 68 HRC. Common steels include carburizing steel (~60 HRc), ball bearing steel (~60 HRc) and tool steel (~68 HRc). Hard types of cast irons include white cast iron (~50 HRc) and ADI/Kymenite (~40 HRc). Construction steel (40–45 HRc), Mn-steel and different types of hardcoatings, i.e. stellite (Stellite is a range of cobalt-chromium alloys designed for wear resistance. The alloys may also contain tungsten or molybdenum and a small but important amount of carbon), P/M steel and cemented carbide also belong to this group. Typically, hard part turning fall within the range of 55–68 HRC.
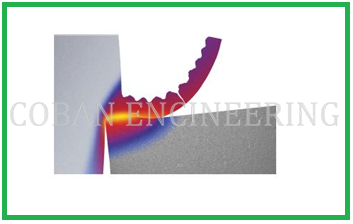
Machinability of the Hardened steel is the smallest group from a machining point of view and finishing is the most common machining operation. Specific cutting force: 369,750-706,150 lbs/inch² (2550–4870 N/mm²). The operation usually produces fair chip control. Cutting forces and power requirements are quite high. The cutting tool material needs to have good resistance to plastic deformation (hot hardness), chemical stability (at high temperatures), mechanical strength and resistance to abrasive wear. CBN has these characteristics and allows turning instead of grinding. Mixed or whisker reinforced ceramic are also used in turning, when the work-piece has moderate surface finish demands and the hardness is too high for carbide. Cemented carbide dominates in milling and drilling applications and is used up to approximately 60 HRc.
Copyright ©2010-2023 Coban Engineering.All Rights Reserved.