- GD&T
GENERAL DIMENSIONING- International Paper Size Standards
- Technical Drawing Styles
- ISO And ANSI Projections
- ANSI Technical Drawing Views
- Technical Drawing Dimesioning Types
- ANSI and ISO Geometric Tolerancing Symbols
- Geometric Tolerancing Reading
- Taylor Principle Rule#1
- Form Tolerances
- Profile Tolerances
- Orientation Tolerances
- Location Tolerances
- Runout Tolerances
- TOLERANCES
ANSI AND ISO- Tolerancing and Engineering Standards
- Hole and Shaft Basis Limits And Fits
- ISO International System For Limits And Fits
- International Tolerance Grade (IT)
- Fundamental Deviations For Hole and Shaft Basis
- ISO Tolerance Band IT01-IT16
- Calculation Of International Tolerance
- Calculation of Upper and Lower Deviation For Shaft
- Calculation of Upper and Lower Deviation For Holes
- ISO Shaft Tolerances (3mm-400mm)
- ISO Shaft Tolerances (400mm-3150mm)
- ISO Hole Tolerances (3mm-400mm)
- ISO Hole Tolerances (400mm-3150mm)
- ANSI Standard Limits and Fits
- METAL CUTTING TECHNOLOGIES
- Terms and Definitions of the Cutting Tools
- Cutting Tool Materials
- Selection of Carbide to machine the work-part
- Identification System For Indexable Inserts
- Work-Part Materials
- Machinability and the specific cutting force
- Machinability of the Certain Material Evaluations
- Cutting Forces and Chip Formations
CUTTING TOOL MATERIALS
Cutting tools must be made of a material harder than the material which is to be cut. The tool must be able to withstand the heat generated in the metal material-cutting process or non-metal material cutting process. Many types of tool materials, ranging from high carbon steel to ceramics and diamonds, are used as cutting tools in today’s metalworking industry. It is important to be aware that differences do exist among tool materials, what these differences are, and the correct application for each type of material. A cutting tool must have the following characteristics in order to produce good quality and economical parts. Hardness, toughness, wear resistance, able to withstand shock during cutting, shaped so edge can penetrate work . Hardness; harness and strength of the cutting tool must be maintained at elevated temperatures, also called hot hardness. Toughness; toughness of cutting tools is needed so that tools don’t chip or fracture, especially during interrupted cutting operations. Wear Resistance; wear resistance means the attainment of acceptable tool life before tools need to be replaced. The various tool manufacturers assign many names and numbers to their products. While many of these names and numbers may appear to be similar, the applications of these tool materials may be entirely different. In most cases, the tool manufacturers will provide tools made of the proper material for each given application.
Carbon Steels : Their use is restricted to the cutting of soft metals and wood. Performance is poor above 250 ℃ (482 ℉). Carbon steel is used primarily to make the less expensive drills, taps, and reamers. Carbon steel is seldom used to make single-point cutting tools. Hardening in carbon steels is very shallow, although some have a small amount of vanadium and chromium added to improve their hardening quality. The cutting speed to use for plain carbon tool steel should be approximately one-half of the recommended speed for high-speed steel.
High-speed Steels: These are used extensively, particularly for multi-point tools.
They have been replaced to a large extent by carbides for single-point tools. Their main application
is for form tools and complex shapes, e.g. for gear cutting and broaching.
They are also used for twist drills, reamers, etc.
Some of the most commonly used alloying elements of high-speed steels are tungsten (W),
molybdenum (Mo), chromium (Cr), vanadium (V), together with carbon (C). There are a number of grades
of high-speed steel that are divided into two types: tungsten high-speed steels and molybdenum high-speed steels.
Tungsten high-speed steels are designated by the prefix letter T before the number that designates the grade.
Molybdenum high-speed steels are designated by the prefix letter M. There is little performance
difference between comparable grades of tungsten or molybdenum high-speed steel.
The addition of 5% to 12 % cobalt to high-speed steel increases its hardness at the temperatures
encountered in cutting, thereby improving its wear resistance and cutting efficiency.
Cobalt slightly increases the brittleness of high-speed steel, making it susceptible to
chipping at the cutting edge. For this reason, cobalt high-speed steels are primarily made
into single-point cutting tools that are used to take heavy roughing cuts in abrasive materials
and through rough abrasive surface scales. The M40 series and T15 are a group of high-hardness or
so-called super high-speed steels that can be hardened to 70 Rc; however, they tend to be
brittle and difficult to grind. For cutting applications, they are usually heat treated to 67–68 Rc
to reduce their brittleness and tendency to chip. The M40 series is appreciably easier to grind than T15.
They are recommended for machining tough die steels and other difficult-to-cut materials; they are
not recommended for applications where conventional high-speed steels perform well. High-speed steels
made by the powder-metallurgy process are tougher and have an improved grind-ability when compared
with similar grades made by the customary process. Tools made of these steels can be hardened
about 1 Rc higher than comparable high-speed steels made by the customary process without a
sacrifice in toughness. They are particularly useful in applications involving intermittent
cutting and where tool life is limited by chipping. All these steels augment rather than replace
the conventional high-speed steels.
They can be hardened to a high initial or room temperature hardness ranging from 63
Rc to 65 Rc for ordinary high-speed steels and up to 70 Rc for the so-called super-high-speed steels.
They can retain sufficient hardness at temperatures up to 1,000 °F to 1,100 °F (538 °C to 593 °C)
to enable them to cut at cutting speeds that will generate these tool temperatures, and they
will return to their original hardness when cooled to room temperature. They harden very deeply,
enabling high-speed steels to be ground to the tool shape from solid stock and to be reground
many times without sacrificing hardness at the cutting edge. High-speed steels can be made
soft by annealing so that they can be machined into complex cutting tools such as drills, reamers,
and milling cutters and then hardened.
CarbidesThey are also called sintered carbides or cemented carbides.
They are harder than high-speed steels and have excellent wear resistance. These consist of powdered
carbides of tungsten, titanium, tantalum, niobium, etc., with powdered cobalt as binder.
They are produced by pressing the powder in dies and sintering at high temperature.
They are then ground to the final shape. They are generally used as tips and can operate up to
1000 °C (1832 °F). Cemented carbides retain a very high degree of hardness at temperatures up to
1400 °F (760 °C) and even higher; therefore, very fast cutting speeds can be used. When used at
fast cutting speeds, they produce good surface finishes on the work-part. Carbides are more
brittle than high-speed steel. Carbides must be used with more care. Hundreds of grades of
carbides are available and attempts to classify these grades by area of application have not
been entirely successfully developed. There are four distinct types of carbides:
a) Titanium Carbides
b) Straight Tungsten carbides
c) Crater-Resistant Carbides
d) Coated Carbides/ Laminated Carbide
Titanium Carbides:These carbides are made entirely from titanium carbide and small amounts of nickel and molybdenum. They have an excellent resistance to cratering and to heat. Their high hot hardness enables them to operate at higher cutting speeds, but they are more brittle and less resistant to mechanical and thermal shock. Therefore, they are not recommended for taking heavy or interrupted cuts. Titanium carbides are less abrasion-resistant and not recommended for cutting through scale or oxide films on steel. Although the resistance to cratering of titanium carbides is excellent, failure caused by crater formation can sometimes occur because the chip tends to curl very close to the cutting edge, thereby forming a small crater in this region that may break through.
Straight Tungsten Carbide: This is the most abrasion-resistant cemented carbide and is used to machine gray cast iron, most nonferrous metals, and nonmetallic materials, where abrasion resistance is the primary criterion. Straight tungsten carbide will rapidly form a crater on the tool face when used to machine steel, which reduces the life of the tool. Titanium carbide is added to tungsten carbide in order to counteract the rapid formation of the crater. In addition, tantalum carbide is usually added to prevent the cutting edge from deforming when subjected to the intense heat and pressure generated in taking heavy cuts.
Crater-Resistant Carbides: These carbides, containing titanium and tantalum carbides in addition to tungsten carbide, are used to cut steels, alloy cast irons, and other materials that have a strong tendency to form a crater.
Coated Carbides / Laminated Carbide: They can be called Laminated Carbide. These consist of a hard thin layer of titanium carbide bonded to a tungsten carbide body. The surface has very high strength at high temperature, whilst the body has high thermal conductivity and thus efficient removal of heat. These are available only as indexable inserts because the coating would be removed by grinding. The principal coating materials are titanium carbide (TiC), titanium nitride (TiN), and aluminum oxide (Al2O3). A very thin layer (approximately 0.0002 in.) of coating material is deposited over a cemented carbide insert; the material below the coating is called the substrate. The overall performance of the coated carbide is limited by the substrate, which provides the required toughness and resistance to deformation and thermal shock. With an equal tool life, coated carbides can operate at higher cutting speeds than uncoated carbides. The increase may be 20 to 30% and sometimes up to 50% faster. Titanium carbide and titanium nitride coated carbides usually operate in the medium (200–800 fpm) cutting speed range, and aluminum oxide coated carbides are used in the higher (800–1600 fpm) cutting speed range. Layer of the coated carbide can be seen in the figure below;
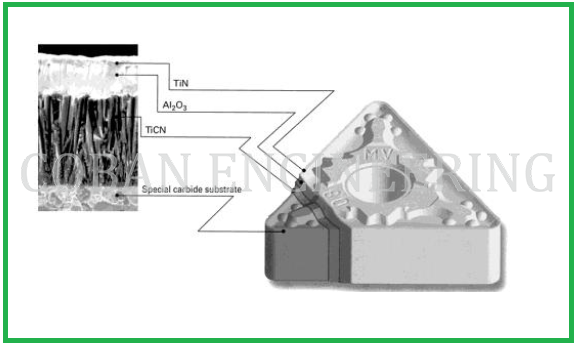
Triple-coated carbide tools provide resistance to wear and plastic deformation in machining of steel, abrasive wear in cast iron, and built-up edge formation. TiC remains as the basic material covering the substrate for strength and wear resistant. The second layer is Al2O3 which has proven chemical stability at high temperatures and resist abrasive wear. The third layer is a thin coating of TiN to give the insert a lower coefficient of friction and to reduce edge build up
Copyright ©2010-2023 Coban Engineering.All Rights Reserved.