- GD&T
GENERAL DIMENSIONING- International Paper Size Standards
- Technical Drawing Styles
- ISO And ANSI Projections
- ANSI Technical Drawing Views
- Technical Drawing Dimesioning Types
- ANSI and ISO Geometric Tolerancing Symbols
- Geometric Tolerancing Reading
- Taylor Principle Rule#1
- Form Tolerances
- Profile Tolerances
- Orientation Tolerances
- Location Tolerances
- Runout Tolerances
- TOLERANCES
ANSI AND ISO- Tolerancing and Engineering Standards
- Hole and Shaft Basis Limits And Fits
- ISO International System For Limits And Fits
- International Tolerance Grade (IT)
- Fundamental Deviations For Hole and Shaft Basis
- ISO Tolerance Band IT01-IT16
- Calculation Of International Tolerance
- Calculation of Upper and Lower Deviation For Shaft
- Calculation of Upper and Lower Deviation For Holes
- ISO Shaft Tolerances (3mm-400mm)
- ISO Shaft Tolerances (400mm-3150mm)
- ISO Hole Tolerances (3mm-400mm)
- ISO Hole Tolerances (400mm-3150mm)
- ANSI Standard Limits and Fits
- METAL CUTTING TECHNOLOGIES
- Terms and Definitions of the Cutting Tools
- Cutting Tool Materials
- Selection of Carbide to machine the work-part
- Identification System For Indexable Inserts
- Work-Part Materials
- Machinability and the specific cutting force
- Machinability of the Certain Material Evaluations
- Cutting Forces and Chip Formations
MACHINABILITY OF THE CERTAIN MATERIALS EVALUATIONS
ISO P; STEEL
Steel materials are comprised mainly of iron and carbon, often with a modest mixture of alloying elements. The biggest difference between cast iron materials and steel is the carbon content. Cast iron materials are compositions of iron and carbon, with a minimum of 1.7 percent carbon to 4.5 percent carbon. Steel has a typical carbon content of .05 percent to 1.5 percent. The commercial production of a significant number of steel grades is further evidence of the demand for this versatile material. Very soft steels are used in drawing applications for automobile fenders, hoods and oil pans, while premium grade high strength steels are used for cutting tools.
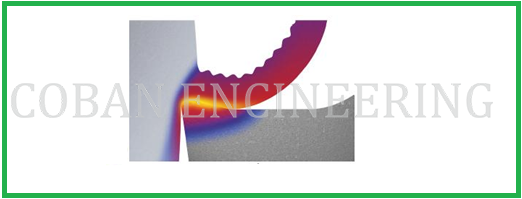
Steels are often selected for their electrical properties or resistance to corrosion. In other applications, non-magnetic steels are selected for wrist watches and minesweepers. The machinability of steel differs, depending on alloying elements, heat treatment and manufacturing process (forged, rolled, cast, etc.).In general, chip control is relatively easy and smooth. Low carbon steels produce longer chips that are sticky and require sharp cutting edges. Specific cutting force kc1: 203,000-449,500 lbs/inch² (1400-3100 N/mm² ). Cutting forces, and thus the power required to machine them, remain within a limited range.
Plain Carbon Steel: This category of steels includes those materials that are a combination of iron and carbon with no alloying elements. As the carbon content in these materials is increased, the ductility (ability to stretch or elongate without breaking) of the material is reduced. Plain carbon steels are numbered in a four-digit code according to the AISI or SAE system (i.e. 10XX). The last two digits of the code indicate the carbon content of the material in hundredths of a percentage point. For example, a 1018 steel has a 0.18-percent carbon content. The plain carbon steel machinability is primarily depending on the carbon content of the work-piece material and its heat treatment. Work-piece Material in the low carbon category is extremely ductile. Ductility of the material creates problem in chip breaking on the turning and drilling operations. This type of work-piece material should be milled with a negative (axial) and Positive (radial) rake angle geometry. Whenever Turning and Drilling operation applied in these work-piece materials negative or neutral cutting tools geometry should be used whenever possible. The plain carbon steel is easy to machine. Difficulties in chip breaking and smearing tendencies (built-up edge) require special attention in low carbon steels (less than 0.25% ). High cutting speeds and sharp edges and/ or geometries, with a positive rake face and thin coated grades, will decrease the smearing tendencies. In turning, it is recommended that the depth of cut remains close to or bigger than the nose radius to improve chip breaking. In general, the machinability is very good for hardened steels; however, they tend to generate relatively large flank wear on the cutting edges.
Alloy Steels: Plain carbon steels are made up primarily of iron and carbon, while alloy steels include these same elements with many other elemental additions. The purpose of alloying steel is either to enhance the material's physical properties or its ultimate manufacturability. The physical property enhancements include improved toughness, tensile strength, hardenability, (the relative ease with which a higher hardness level can be attained), ductility and wear resistance. The use of alloying elements can alter the final grain size of a heat-treated steel, which often results in a lower machinability rating of the final product. The primary types of alloyed steel are: nickel, chromium, manganese, vanadium, molybdenum, chrome-nickel, chrome-vanadium, chrome-molybdenum, and nickel-molybdenum. The following material, when they added to the carbon steel they change physical and mechanical properties for alloyed carbon steel.
Aluminum: This acts as a deoxidizer to increase resistance to oxidation and scaling. It aids nitriding, restricts grain growth, and may reduce strength unless in small quantities. The range used is 0-2%.
Chromium: A range of 0.3-4%, improves wear, oxidation, scaling resistance, strength and hardenability. It also increases high-temperature strength, but with some loss of ductility. Chromium combines with carbon to form a wear-resistant microstructure. Above 12% the steel is stainless; up to 30% it is used.
Cobalt: Cobalt provides air hardening and resistance to scaling. It improves the cutting properties of tool steel with 8-10%. With chromium, cobalt gives certain high alloy steels high-temperature scaling resistance.
Copper: The typical range is 0.24.5%. It has limited application for improving corrosion resistance and yield strength of low alloy steels and promotes a tenacious oxide film.
Lead: Up to 0.25% is used. It increases machineability in plain carbon steels rather than in alloy steels.
Manganese: The range used is 0.3-2%. It reduces Sulphur brittleness, is Pearlitic up to 2%, and a hardening agent up to 1%. From 1-2% it improves strength and toughness and is non-magnetic above 5%.
Molybdenum: The range used is 0.3-5%. It is a carbide forming element which promotes grain refinement and increases high-temperature strength, creep resistance, and hardenability. Molybdenum reduces temper brittleness in nickel-chromium steels.
Nickel: The range used is 0.3-5%. It improves strength, toughness and hardenability, without affecting ductility. A high proportion of it improves corrosion resistance. For parts subject to fatigue 5% is used, and above 27% the steel is non-magnetic. Nickel promotes an austenitic structure.
Silicon: The usual range is 0.2-3%. It has little effect below 3%. At 3% it improves strength and hardenability but reduces ductility. Silicon acts as a deoxidizer.
Sulphur: Up to 0.5% sulphur forms sulphides which improve machineability but reduces ductility and weldability.
Titanium: This is a strong carbide forming element. In proportions of 0.2-0.75%, it is used in steels to make them age-hardening and to give high strength. It stabilizes austenitic stainless steel.
Tungsten: This forms hard stable carbides and promotes grain refining with great hardness and toughness at high temperatures. It is a main alloying element in high speed tool steels. It is also used for permanent-magnet steels.
Vanadium: This is a carbide forming element and deoxidizer used with nickel and/or chromium to increase strength. It improves hardenability and grain refinement and combines with carbon to form wear-resistant micro-constituents. As a deoxidizer it is useful for casting steels, improving strength and hardness and eliminating blowholes, etc. Vanadium is used in high-speed and pearlitic chromium steels.
The machinability consideration of the Alloy Steel varies widely. It depends on their hardness and chemical composition. The correct geometry of the cutting tools selections for alloyed steels are often totally dependent on the parts hardness. In Milling operation positive (radial) or negative axial geometries are preferred on alloyed steel materials due to their toughness and strength. In turning operations double negative or neutral geometries should be preferred on softer alloyed work-part materials. The tool with lead angle should be used on these work-part materials whenever possible to minimize the shock associated with cutting tool entry into the work-part. Machinability for low alloyed steels depends on the alloy content and heat treatment (hardness). For all materials in the group, the most common wear mechanisms are crater and flank wear. Hardened materials give higher heat in the cutting zone and can result in plastic deformation of the cutting edge. In general, machinability decreases at higher alloy contents and hardness. For example, at 12-15% alloying elements and hardness up to 450 HB, the cutting edge needs good heat resistance to withstand plastic deformation.
Tool Steel: This group of high strength steels is often used in the manufacture of cutting tools for metals, wood and other work-piece materials. In addition, these high-strength materials are used as die and punch materials due to their extreme hardness and wear resistance after heat treatment. The key to achieving the hardness, strength and wear-resistance desired for any tool steel is normally through careful heat treatment. These materials are available in a wide variety of grades with a substantial number of chemical compositions designed to satisfy specific as well as general application criteria
Refractory Alloys: These group of materials designated as refractory alloys includes those metals which contain high concentrations of their W (Tungsten), Ta (Tantalum), Mo ( molybdenum), or Co ( Columbium). These materials are known for their heat resistance properties, which allow them to operate in extreme thermal environments without permanent damage. They are being known for their extremely high melting points and abrasiveness. Most of these materials are quite brittle. They possess very low machinability ratings when their heat resistance and extreme melting point properties are considered. The machining of these groups of the material is characterized by extremely low cutting speed and feed rates when utilizing carbide cutting tools. Cast Molybdenum has a machinability rating of approximately 30% whereas pure Tungsten has a rating of only 5%. The machinability of Tantalum and Columbium is at a more moderate level and thus falls between these two materials.
Copyright ©2010-2023 Coban Engineering.All Rights Reserved.