- GD&T
GENERAL DIMENSIONING- International Paper Size Standards
- Technical Drawing Styles
- ISO And ANSI Projections
- ANSI Technical Drawing Views
- Technical Drawing Dimesioning Types
- ANSI and ISO Geometric Tolerancing Symbols
- Geometric Tolerancing Reading
- Taylor Principle Rule#1
- Form Tolerances
- Profile Tolerances
- Orientation Tolerances
- Location Tolerances
- Runout Tolerances
- TOLERANCES
ANSI AND ISO- Tolerancing and Engineering Standards
- Hole and Shaft Basis Limits And Fits
- ISO International System For Limits And Fits
- International Tolerance Grade (IT)
- Fundamental Deviations For Hole and Shaft Basis
- ISO Tolerance Band IT01-IT16
- Calculation Of International Tolerance
- Calculation of Upper and Lower Deviation For Shaft
- Calculation of Upper and Lower Deviation For Holes
- ISO Shaft Tolerances (3mm-400mm)
- ISO Shaft Tolerances (400mm-3150mm)
- ISO Hole Tolerances (3mm-400mm)
- ISO Hole Tolerances (400mm-3150mm)
- ANSI Standard Limits and Fits
- METAL CUTTING TECHNOLOGIES
- Terms and Definitions of the Cutting Tools
- Cutting Tool Materials
- Selection of Carbide to machine the work-part
- Identification System For Indexable Inserts
- Work-Part Materials
- Machinability and the specific cutting force
- Machinability of the Certain Material Evaluations
- Cutting Forces and Chip Formations
ORIENTATION TOLERANCES
Orientation Tolerances can be state by three tolerance zone. These are Perpendicularity, Angularity, and Parallelism. Perpendicularity is 90° to a datum and parallelism is 0° to a datum. Angularity controls a surface (non feature of size), a center plane or an axis of a feature of size to a specified angle. These tolerances control the orientation of features to a datum plane or axis. Orientation Tolerances are related to datums. LMC or MMC can apply to feature of size of the orientation tolerances.
Perpendicularity:
Perpendicularity tolerance symbol is shown as "⊥".Perpendicularity tolerance is a three-dimensional geometric tolerance that controls how much a surface, axis, or plane can deviate from a 90 degree angle or it is can be defined as a condition of a surface, median plant, or axis at 90 degree to a datum plane or axis. A tolerance zone with Perpendicularity can be defined by two parallel plane perpendicular to a datum plane, datum axis, or axis is within where the surface of the feature must lie. The difference is that perpendicularity specifies a 90-degree angle between features while parallelism defines two features that must remain parallel to each other. LMC or MMC can apply to feature of size.
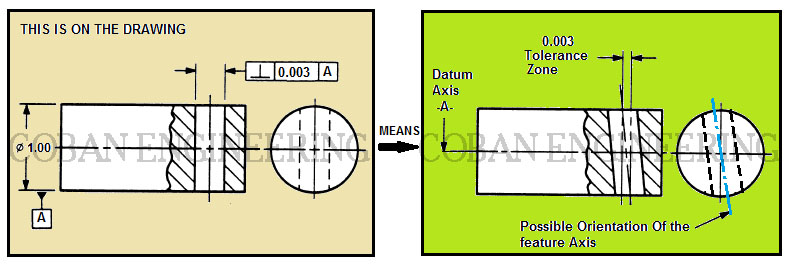
The feature of the part axis must lie between two parallel planes 0.003 apart which are perpendicular to datum A. The feature of the part axis must be within specified tolerance limit.
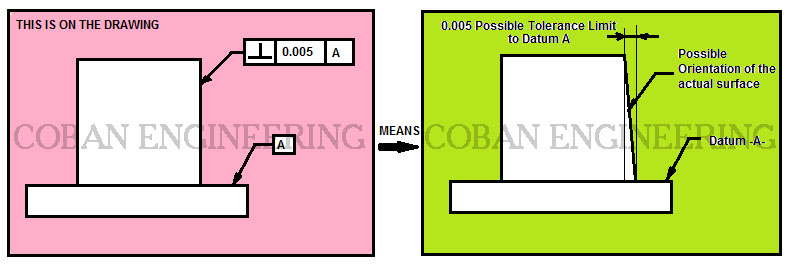
The feature of the part Plane must lie between two parallel planes 0.005 apart which are perpendicular to datum A. The feature of the part plane must be within specified tolerance limit.
Angularity:
Angularity tolerance symbol is shown as "∠".Angularity tolerance specifies a tolerance zone defined by two parallel plane at the specified angle other than 90 degree from a datum plane or axis within where the surface or the axis of the feature must lie. Also Angularity tolerance zone can be defined as a three-dimensional geometric tolerance that controls how much a surface, axis, or plane can deviate from the angle described in the design specifications. LMC or MMC can apply to feature of size.
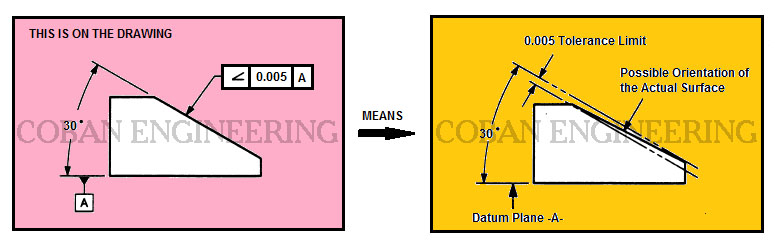
The machined surface must lie between two parallel planes 0.005 apart which are dispositoned at 30 degree angle to Datum -A- .The machined surface must be within the specified tolerance limit.
Parallelism:
Parallelism symbol is shown as " ⁄⁄". Parallelism tolerance zone is the condition of a surface or center plane equidistant at all points from a datum plane, or an axis. The distance between the parallel lines, or surfaces, is specified by the geometric tolerance zone. Parallelism can be also specified a tolerance zone defined by two parallel planes or lines parallel to a datum plane or axis, respectively, within where the surface or axis of the feature must lie.LMC or MMC can apply to feature of size.
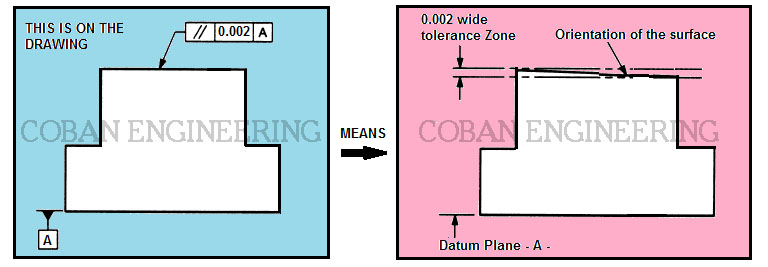
The surface of the part must lie between two parallel planes 0.002 apart around the axis which are parallel to the datum plane A. The surface of the part must be within specified tolerance limit.
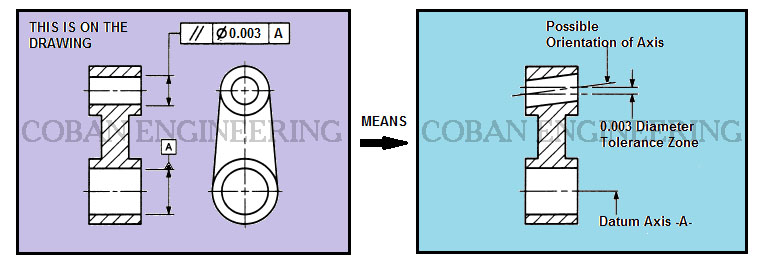
The feature axis must lie within 0.003 diameter of cylindrical zone parallel to the datum axis A. The feature axis must be within specified tolerance limit.
Copyright ©2010-2023 Coban Engineering.All Rights Reserved.