- GD&T
GENERAL DIMENSIONING- International Paper Size Standards
- Technical Drawing Styles
- ISO And ANSI Projections
- ANSI Technical Drawing Views
- Technical Drawing Dimesioning Types
- ANSI and ISO Geometric Tolerancing Symbols
- Geometric Tolerancing Reading
- Taylor Principle Rule#1
- Form Tolerances
- Profile Tolerances
- Orientation Tolerances
- Location Tolerances
- Runout Tolerances
- TOLERANCES
ANSI AND ISO- Tolerancing and Engineering Standards
- Hole and Shaft Basis Limits And Fits
- ISO International System For Limits And Fits
- International Tolerance Grade (IT)
- Fundamental Deviations For Hole and Shaft Basis
- ISO Tolerance Band IT01-IT16
- Calculation Of International Tolerance
- Calculation of Upper and Lower Deviation For Shaft
- Calculation of Upper and Lower Deviation For Holes
- ISO Shaft Tolerances (3mm-400mm)
- ISO Shaft Tolerances (400mm-3150mm)
- ISO Hole Tolerances (3mm-400mm)
- ISO Hole Tolerances (400mm-3150mm)
- ANSI Standard Limits and Fits
- METAL CUTTING TECHNOLOGIES
- Terms and Definitions of the Cutting Tools
- Cutting Tool Materials
- Selection of Carbide to machine the work-part
- Identification System For Indexable Inserts
- Work-Part Materials
- Machinability and the specific cutting force
- Machinability of the Certain Material Evaluations
- Cutting Forces and Chip Formations
ISO M; STAINLESS STEEL
Stainless Steels: As the name implies, this group of materials is designed to resist oxidation and other forms of corrosion, in addition to heat in some instances. These materials tend to have significantly greater corrosion resistance than their plain or alloy steel counterparts due to the substantial additions of chromium as an alloying element. Stainless steels are used extensively in the food processing, chemical and petroleum industries to transfer corrosive liquids between processing and storage facilities..

Stainless steels can be cold formed, forged, machined, welded or extruded. This group of materials can attain relatively high strength levels when compared to plain carbon and alloy steels. Stainless steels are available in up to 150 different chemical compositions. The wide selection of these materials is designed to satisfy the broad range of physical properties required by potential customers and industries. Stainless steels fall into four distinct metallurgical categories. These categories include; austenitic, ferritic, martensitic, and precipitation hardening steels. Austenitic steels which is known as 300 series steel are generally difficult to machine. It could have chattering problem, high stiffness cutting tools required for this type of work-piece material. Ferritic stainless steel which is known also 300 series steels have good machinability. Martensitic steels which are known 400 series are abrasive and tend to form build-up edges. The tools for these kinds of work-piece material should have high hardness and crater-wear resistance. Precipitation hardening stainless steels are strong and abrasive.
Machinability in general with Stainless Steel; The machinability of stainless steels differs depending on alloying elements, heat treatment and manufacturing processes (forged, cast, etc.) In general, machinability decreases with a higher alloy content, but free-machining or machinability improved materials are available in all groups of stainless steels. Long-chipping material. Chip control is fair in ferritic/martensitic materials, becoming more complex in the austenitic and duplex types. Specific cutting force: 1800-2850 N/mm² . Machining creates high cuttting forces, built-up edge, heat and work-hardened surfaces. Higher nitrogen (N) content austenitic structure, it increases strength and provides some resistance against corrosion, but lowers machinability, while the deformation hardening increases. Additions of Sulphur (S) are used to improve machinability. High Carbon content (more than 0.2%) provides relatively large flank wear. Mo and N decrease machinability, however, they provide resistance to acid attacks and contribute to high temperature strength. Machinability of the Ferritic, Martensitic, and Austenitic and super-austenitic stainless steel; Generally, the machinability is good and very similar to low alloyed steels, therefore it is classified as an ISO P material. High carbon content (>0.2%) enables hardening of the material. Machining will create flank and crater wear with some built-up edge. ISO P grades and geometries work well. Work hardening produces hard surfaces and hard chips , which in turn lead to notch wear. It also creates adhesion and produces built-up edge. It has a relative machinability of 60%. The hardening condition can tear coating and substrate material from the edge, resulting in chipping and bad surface finish. Austenite produces tough, long, continuous chips, which are difficult to break. Adding S improves machinability, but results in lowered resistance to corrosion. Use sharp edges with a positive geometry. Cut under the work hardened layer. Keep cutting depth constant. Generate a lot of heat when machined.
ISO K; CAST IRON
Cast Iron: All metals that contain "Fe" are known as ferrous materials. The word "ferrous" is by definition, "relating to or containing iron." Ferrous materials include cast iron, pig iron, wrought iron, and low carbon and alloy steels. The extensive use of cast iron and steel work-piece materials can be attributed to the fact that iron is one of the most frequently occurring elements in nature. When iron ore and carbon are metallurgically mixed, a wide variety of work-piece materials result with a fairly unique set of physical properties. Carbon contents are altered in cast irons and steels to provide changes in hardness, yield and tensile strengths. The physical properties of cast irons and steels can be modified by changing the amount of the iron-carbon mixtures in these materials as well as their manufacturing process. Pig iron is created after iron ore is mixed with carbon in a series of furnaces. This material can be changed further into cast iron, steel or wrought iron depending on the selected manufacturing process.
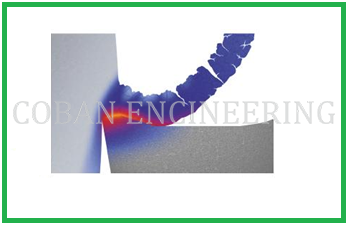
Cast iron is an iron carbon mixture that is generally used to pour sand castings, as opposed to making billets or bar stock. It has excellent flow properties and therefore, when it is heated to extreme temperatures, is an ideal material for complex cast shapes and intricate molds. This material is often used for automotive engine blocks, cylinder heads, valve bodies, manifolds, heavy equipment oil pans and machine bases.
Gray Cast Iron: Gray cast iron is an extremely versatile, very machinable relatively low strength cast iron used for pipe, automotive engine blocks, farm implements and fittings. This material receives its dark gray color from the excess carbon in the form of graphite flakes, which give it its name. This type of work-piece has relatively low hardness and low strength levels. Their tendency is to produce short discontinuous chips. These kinds of material can be machined by using double-negative or negative (axial) and positive (radial) rake angle geometries cutting tools. Because of short discontinuous chips, the entire cutting force is concentrated on a very narrow area of the cutting tool edge.
White Cast Iron: White cast iron occurs when all of the carbon in the casting is combined with iron to form cementite. This is an extremely hard substance that results from the rapid cooling of the casting after it is poured. Since the carbon in this material is transformed into cementite, the resulting color of the material when chipped or fractured is a silvery white. Thus the name white cast iron. However, white cast iron has almost no ductility, and therefore when it is subjected to any type of bending or twisting loads, it fractures. The hard brittle white cast iron surface is desirable in those instances where a material with extreme abrasion resistance is required. Applications of this material would include plate rolls in a mill or rock crushers. Due to the extreme hardness of the material, it is very difficult to machine. Double negative insert geometries are almost exclusively required for these types of material. Their Brinell hardness is 450-500.
Malleable Cast Iron: When white cast iron castings are annealed (softened by heating to a controlled temperature for a specific length of time), malleable iron castings are formed. Malleable iron castings result when hard, brittle cementite in white iron castings is transformed into tempered carbon or graphite in the form of rounded nodules or aggregate. The resulting material is a strong, ductile, tough and very machinable product that is used on a broad scope of applications. It is to machine compare to white iron casting. Malleable cast iron tendency also is to produce short and discontinuous chips. Double negative-negative (axial) and Positive (radial) rake angle geometries can be used to machine these types of materials.
Nodular Cast Iron: Nodular or "ductile" iron is used to manufacture a wide range of automotive engine components including cam shafts, crank shafts, bearing caps and cylinder heads. This material is also frequently used for heavy equipment cast parts as well as heavy machinery faceplates and guides. Nodular iron is strong, ductile, tough and extremely shock resistant. Nodular cast irons are very machinable compare to gray cast iron. Double negative or positive (radial) and negative (axial) rake angles cutting tools are normally used to machine these types of material.
Machinability of Malleable cast iron, Grey cast iron, and Nodular Cast Iron, Compacted Graphite Iron, Austempered Ductile Iron; Malleable cast iron has a higher tensile strength compared to GCI, and resembles NCI in its machinability, but both have generally excellent machining properties. In general cast iron with a perlitic struture increases the abrasive wear, while ferritic structures increase the adhesive wear. Grey cast iron has low impact strength, generates low cutting forces and the machinability is very good. Wear is created in the cutting process only by abrasion; there is no chemical wear. Grey cast iron is often alloyed with Cr in order to improve the mechanical properties. The higher strength will then result in decreased machinability. Nodular cast iron has a strong tendency to form built-up edge. This tendency is stronger for the softer NCI materials with higher ferritic contents. When machining components with high ferritic contents and with interrupted cuts, adhesion wear is often the dominating wear mechanism. This can cause problems with flaking of the coating. The adhesion problem is less pronounced with harder NCI (Nodular Cast Iron) materials that have a higher perlitic content. Here abrasive wear and/or plastic deformation are more likely to occur. From a machinability point of view compacted graphite iron is between grey and nodular cast iron. With two to three times the tensile strength of grey cast iron and lower thermal conductivity machining of CGI (Compacted Graphite Iron) generates higher cutting forces and more heat in the cutting zone. An increased content of titanium in the CGI material influences tool life negatively. The most common machining operations are face milling and cylinderboring. Instead of cylinderboring a change of method to circular milling can improve both the tool life and the productivity. A 40-50% reduction in tool-life compared to NCI can be expected. Tensile strength and ductility of ADI are near to steel, but the chip formation process classifies ADI (Austempered Ductile Iron) as a ductile iron (segmented chip formation). The micro hardness of ADI is higher, when compared to steels of comparable hardness. Higher ADI grades contain hard particles in the micro-structure. High thermal and mechanical loads, due to high strength and ductility, will concentrate wear near the cutting edge, due to the segmented chip formation process, and wear on the top rake. Hardening during chip formation results in high dynamic cutting forces. The cutting-edge temperature is a strong factor for determining wear
Copyright ©2010-2023 Coban Engineering.All Rights Reserved.