- GD&T
GENERAL DIMENSIONING- International Paper Size Standards
- Technical Drawing Styles
- ISO And ANSI Projections
- ANSI Technical Drawing Views
- Technical Drawing Dimesioning Types
- ANSI and ISO Geometric Tolerancing Symbols
- Geometric Tolerancing Reading
- Taylor Principle Rule#1
- Form Tolerances
- Profile Tolerances
- Orientation Tolerances
- Location Tolerances
- Runout Tolerances
- TOLERANCES
ANSI AND ISO- Tolerancing and Engineering Standards
- Hole and Shaft Basis Limits And Fits
- ISO International System For Limits And Fits
- International Tolerance Grade (IT)
- Fundamental Deviations For Hole and Shaft Basis
- ISO Tolerance Band IT01-IT16
- Calculation Of International Tolerance
- Calculation of Upper and Lower Deviation For Shaft
- Calculation of Upper and Lower Deviation For Holes
- ISO Shaft Tolerances (3mm-400mm)
- ISO Shaft Tolerances (400mm-3150mm)
- ISO Hole Tolerances (3mm-400mm)
- ISO Hole Tolerances (400mm-3150mm)
- ANSI Standard Limits and Fits
- METAL CUTTING TECHNOLOGIES
- Terms and Definitions of the Cutting Tools
- Cutting Tool Materials
- Selection of Carbide to machine the work-part
- Identification System For Indexable Inserts
- Work-Part Materials
- Machinability and the specific cutting force
- Machinability of the Certain Material Evaluations
- Cutting Forces and Chip Formations
2-) Locational Fits [LC,LT,LN]:
Locational Clearance Fits are divided into three groups. these fits are intended to determine only the location of the mating parts. They may provide accurate or rigid location like interference fit or some freedom of location like clearance fit. These three fits are Locational Clearance Fits (LC), Locational Transition Fits (LT), Interference Fits (LN). Locational Fits are not for running machinery, it is for location of the mating parts. Some example: Parts of machines fixed to shafts using pins, bearing bushings, precise fits of machines and preparations, exchangeable wheels, bolts, retaining and distance rings, parts of machines fixed to shafts using pins, rivets or welds, etc
a-) Locational Clearance Fits [LC]: This kind of fits are for parts which are normally stationary but which can be freely assembled and disassembled. With Locational clearance fits, parts run from snug fits for parts requiring accuracy of location through the medium clearance to the looser fastener fits where freedom of assembly is necessary. The coupled parts must be fixed mechanically to prevent any moving part against the other during assembly. Some of the use for this fits are bearing bushings, exchangeable wheels, bolts, retaining and distance rings, rivets, parts of machines fixed to shafts using pins, or welds, etc. The lower the class like LC1, LC2 for the precise guiding and centering of parts, the higher the class like LC10, LC11 for the free fits with great clearances and maximum tolerances.The tolerance of mating parts and fit clearance increases with increasing class of the fit. Tighter than RC fits, but the shaft and hole may be the same size. LC fits allow the shaft to be located more accurately than the RC fits but may still be loose. SHAFT "d9" with Hole "H8" is generally suitable for loose running fits such as Plummer block bearing and loose pulleys. SHAFT "e8" with Hole "H8" is recommended for general loose clearance fits and for properly lubricated bearings requiring appreciable clearance. SHAFT "f7" with Hole "H7" and " f8" with Hole "H8" are recommended to provide a normal running fits. This fit is widely used a normal grease-lubricated or oil-lubricated bearing where no substantial temperature differences are encountered. Typical applications are gear box shaft bearings and small electrical motor and pump bearings. SHAFT "g5" with Hole "H6" and "g6" with Hole "H7" are expensive to manufacture since the clearances are small and they are not recommended for running fits except in precision equipment where shaft loadings are very light. Typical applications are the bearings for accurate link work and for piston and slide valves. in addition, they are often used for spigot or location fits. SHAFT "h7" with Hole "H8" has an upper limit of zero although in practice a slight clearance will usually be found. it is used for non-running parts and is useful for normal location and spigot fits and may be used as a precision fit.
Graphical Representation of ANSI B4.1-1967 Locational Clearance Fits Table
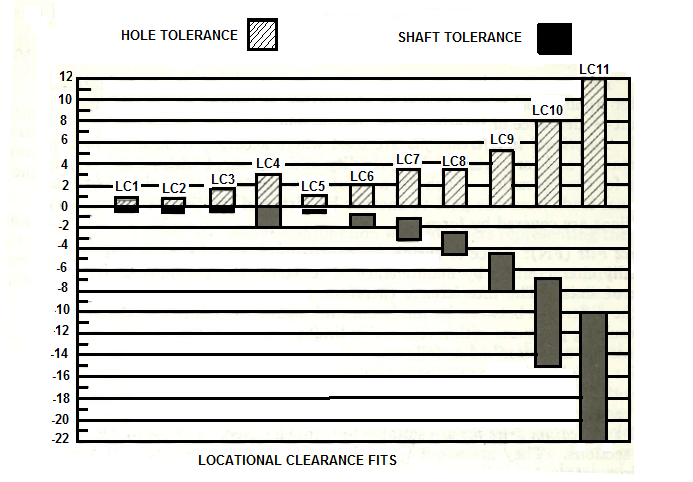
Locational Clearance Limits and Fits For Cylindrical Parts
[(ANSI B4.1-1967,R1987)][Table LC1-LC5]
All limits shown in chart below are in thousandths of an inches. Symbols H6,H7,s6, etc. are Shaft and Hole designations used in American-British-Canadian System (ABC). Limits for Shaft and Hole are applied algebraically to the Nominal (basic) size to obtain the limits of the size for the parts. All data given in bold in the chart below are in accordance with ABC agreements. The values given under the "Clearance Limits Column" represent min and max amounts of clearance resulting from application of standard tolerance limits.
VALUES SHOWN BELOW ARE IN THOUSANDTHS OF AN INCHES | ||||||||||||||||
Nominal (Basic) Size Ranges (Inches) |
Class LC1 | Class LC2 | Class LC3 | Class LC4 | Class LC5 | |||||||||||
Clearance Limits | Standard Tolerance Limits | Clearance Limits | Standard Tolerance Limits | Clearance Limits | Standard Tolerance Limits | Clearance Limits |
Standard Tolerance Limits | Clearance Limits | Standard Tolerance Limits | |||||||
Over | To | Hole H6 | Shaft h5 | Hole H7 | Shaft h6 |
Hole H8 | Shaft h7 | Hole H10 | Shaft h9 | Hole H7 | Shaft g6 |
|||||
0 | 0.12 | 0 0.45 | +0.25 0 | 0 -0.2 | 0 0.65 | +0.4 0 |
0 -0.25 | 0 -0.25 | 0 1.0 | +0.6 0 | 0 -0.4 | 0 2.6 |
+1.6 0 | 0 -1.0 | 0.1 0.75 | -0.1 -0.35 |
0.12 | 0.24 | 0 0.5 | +0.3 0 | 0 -0.2 | 0 0.8 | +0.5 0 |
0 -0.3 | 0 1.2 | +0.7 0 | 0 -0.5 | 0 3.0 | +1.8 0 |
0 -1.2 | 0.15 0.95 | +0.5 0 | -0.15 -0.45 |
0.24 | 0.40 | 0 0.65 | +0.4 0 | 0 -0.25 | 0 1.0 | +0.6 0 |
0 -0.4 | 0 1.5 | +0.9 0 | 0 -0.6 | 0 3.6 | +2.2 0 |
0 -1.4 | 0.2 1.2 | +0.6 0 | -0.2 -0.6 |
0.40 | 0.71 | 0 0.7 | +0.4 0 | 0 -0.3 | 0 1.1 | +0.7 0 |
0 -0.4 | 0 1.7 | +1.0 0 | 0 -0.7 | 0 4.4 | +2.8 0 |
0 -1.6 | 0.25 1.35 | +0.7 0 | -0.25 -0.65 |
0.71 | 1.19 | 0 0.9 | +0.5 0 | 0 -0.4 | 0 1.3 | +0.8 0 |
0 -0.5 | 0 2.0 | +1.2 0 | 0 -0.8 | 0 5.5 | +3.5 0 |
0 -2.0 | 0.3 1.6 | +0.8 0 | -0.3 -0.8 |
1.19 | 1.97 | 0 1.0 | +0.6 0 | 0 -0.4 | 0 1.6 |
1.0 0 | 0 -0.6 | 0 2.6 | +1.6 0 | 0 -1.0 | 0 6.5 | +4.0 0 | 0 -2.5 | 0.4 2.0 | +1.0 0 |
-0.4 -1.0 |
1.97 | 3.15 | 0 1.2 | +0.7 0 | 0 -0.5 | 0 1.9 | +1.2 0 |
0 -0.7 | 0 3.0 | +1.8 0 | 0 -1.2 | 0 7.5 | +4.5 0 |
0 -3.0 | 0.4 2.3 | +1.2 0 | -0.4 -1.1 |
3.15 | 4.73 | 0 1.5 | +0.9 0 | 0 -0.6 | 0 2.3 | +1.4 0 |
0 -0.9 | 0 3.6 | +2.2 0 | 0 -1.4 | 0 8.5 | +5.0 0 |
0 -3.5 | 0.5 2.8 | +1.4 0 | -0.5 -1.4 |
4.73 | 7.09 | 0 1.7 | +1.0 0 | 0 -0.7 | 0 2.6 | +1.6 0 |
0 -1.0 | 04.1 | +2.5 0 | 0 -1.6 | 0 10.0 | +6.0 0 |
0 -4.0 | 0.6 3.2 | +1.6 0 | -0.6 -1.6 |
7.09 | 9.85 | 0 2.0 | +1.2 0 | 0 -0.8 | 0 3.0 | +1.8 0 |
0 -1.2 | 0 4.6 | +2.8 0 | 0 -1.8 | 0 11.0 | +7.0 0 |
0 -4.5 | 0.6 3.6 | +1.8 0 | -0.6 -1.8 |
9.85 | 12.41 | 0 2.1 | +1.2 0 | 0 -0.9 | 0 3.2 | +2.0 0 |
0 -1.2 | 0 5.0 | +3.0 0 | 0 -2.0 | 0 13.0 | +8.0 0 |
0 -5.0 | 0.7 3.9 | +2.0 0 | -0.7 -1.9 |
12.41 | 15.75 | 0 2.4 | +1.4 0 | 0 -1.0 | 0 3.6 | +2.2 0 |
0 -1.4 | 0 5.7 | +3.5 0 | 0 -2.2 | 0 15.0 | +9.0 0 |
0 -6.0 | 0.7 4.3 | +2.2 0.0 | -0.7 -2.1 |
15.75 | 19.69 | 0 2.6 | +1.6 0 | 0 -1.0 | 0 4.1 | +2.5 0 |
0 -1.6 | 0 6.5 | +4.0 0 | 0 -2.5 | 0 16.0 | +10.0 0 |
0 -6.0 | 0.8 4.9 | +2.5 0 | -0.8 -2.4 |
19.69 | 30.09 | 0 3.2 | +2.0 0 | 0 -1.2 | 0 5.0 | +3.0 0 | 0 +2.0 |
0 8.0 | +5.0 0 | 0 -3.0 | 0 20.0 | +12.0 0 | 0 -8.0 | 0.9 5.9 |
+3.0 0 | -0.9 -2.9 |
30.09 | 41.49 | 0 4.1 | +2.5 0 | 0 -1.6 | 0 6.5 | +4.0 0 | 0 -2.5 |
0 10.0 | +6.0 0 | 0 -4.0 | 0 26.0 | +16.0 0 |
0 -10.0 | 1.0 7.5 | +4.0 0 | -1.0 -3.5 |
41.49 | 56.19 | 0 5.0 | +3.0 0 | 0 -2.0 | 0 8.0 | +5.0 0 | 0 -3.0 |
0 13.0 | +8.0 0 | 0 -5.0 | 0 32.0 | +20.0 0 | 0 -12.0 |
1.2 9.2 | +5.0 0 | -1.2 -4.2 |
56.19 | 76.39 | 0 6.5 | +4.0 0 | 0 -2.5 | 0 10.0 | +6.0 0 | 0 -4.0 |
0 16.0 | +10.0 0 | 0 -6.0 | 0 41.0 | +25.0 0 | 0 -16.0 |
1.2 11.2 | 6.0 0 | -1.2 -5.2 |
76.39 | 100.9 | 0 8.0 | -5.0 0 | 0 -3.0 | 0 13.0 | +8.0 0 | 0 -5.0 |
0 20.0 | +12.0 0 | 0 -8.0 | 0 50.0 | +30.0 0 | 0 -20.0 |
1.4 14.4 | +8.0 0 | -1.4 -6.4 |
100.9 | 131.9 | 0 10.0 | +6.0 0 | 0 -4.0 | 0 16.0 | +10.0 0 | 0 -6.0 |
0 26.0 | +16.0 0 | 0 -10.0 | 0 65.0 | +40.0 0 | 0 -25.0 |
1.6 17.6 | +10.0 0 | -1.6 -7.6 |
131.9 | 171.9 | 0 13.0 | +8.0 | 0 -5.0 | 0 20.0 | +12.0 0 | 0 -8.0 |
0 32.0 | +20.0 0 | 0 -12.0 | 0 80.0 | +50.0 0 | 0 -30.0 |
1.8 21.8 | +12.0 0 | -1.8 -9.8 |
171.9 | 200 | 0 16.0 | +10.0 0 | 0 -6.0 | 0 26.0 | +16.0 0 | 0 -10.0 |
0 41.0 | +25.0 0 | 0 -16.0 | 0 100 | +60.0 0 | 0 -40.0 |
1.8 27.8 | 16.0 0 | -1.8 -11.8 |
Copyright ©2010-2023 Coban Engineering.All Rights Reserved.